Introduction
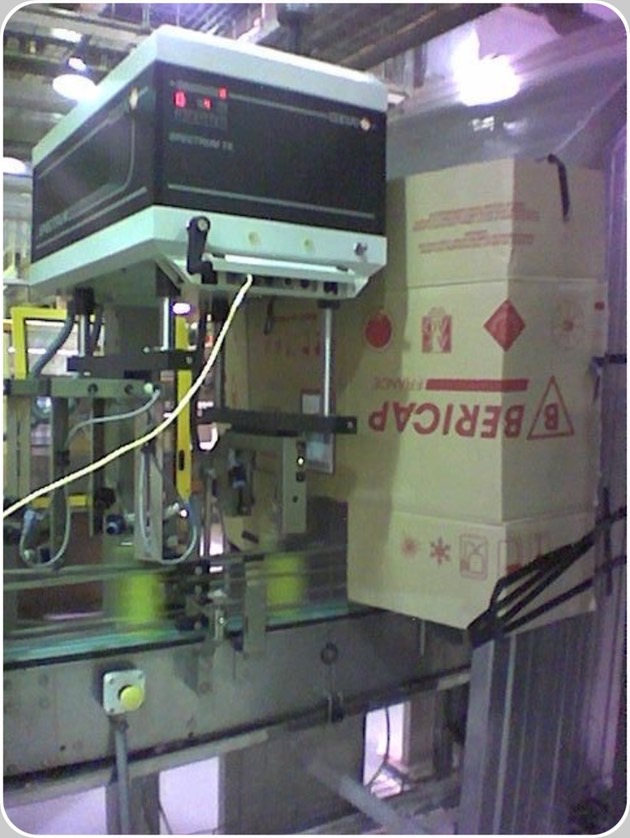
Powerade™ is a famous energy beverage, the first in a row of energy drinks with great success launched in the World, after 1988. Some years ago, The Coca-Cola Company™ updated the bottles of the standard Powerade to a new sport-grip bottle. We were in a historic Packaging Plant, in the outskirts of one of the greatest capitol towns of the World, when The Coca-Cola Company started to test there, 12000 km far from the USA, its new sleeved product. The Case we’ll describe happened in a past epoch. Today there is widespread consensus on a key point. Sleeved containers cannot be inspected at all for sleeve’s position and conditions, by mean of general purpose digital (on-off) Label Presence photoscanners whose only advantage is to be cheap.
When the initial production of Powerade® started, the Label Presence electronic inspector, considering them not labelled, immediately rejected ~50 % of all the correctly sleeved containers. Someone attributed to the nearby (~25 cm) presence of the Warmer Machine, visible at right side of the Inspector, the root cause for the Inspector’s malfunction. Applying a big non-professional looking cardboard as thermal insulator, did not solved the problem
With and without cardboard
…someone attributed to the nearby (~250 mm) presence of the Warmer Machine, visible at right side of the Inspector, the root cause for the Inspector’s malfunction
When the initial production of Powerade® started, the Label Presence electronic inspector, considering them not labelled, immediately rejected ~50 % of all the correctly sleeved containers. Someone attributed to the nearby (~250 mm) presence of the Warmer Machine, visible at right side of the Inspector, the root cause for the Inspector’s malfunction.

Applying a big (non-professionally looking) cardboard as a thermal insulator, did not solved the problem. Then, someone else started to conjecture that, maybe, the cardboard thickness was not enough to insulate thermically the Warmer Machine and Electronic Inspector. We returned on site observing the anomaly and starting by placing ourselves a question: if the Label Inspector had no problem to recognise the bottles non-labelled, why should now reject so many correctly labelled ? Who preceded us really had what seemed a reasonable answer:
“Until now we were not applying sleeves, because not producing Powerade®, rather other aseptically filled beverages with common wrap around labels. Then, until now the Warmer Machine set immediately before the Inspector was off and at thermal equilibrium with the ambient”.
In other words, who thinked this Root Cause for the observed Effect, Inspector’s massive false rejects when checking Powerade® and only Powerade®, was convinced that an interference existed between the Label Presence Photoscanners and the source of thermal energy represented by a powered Warmer Machine.
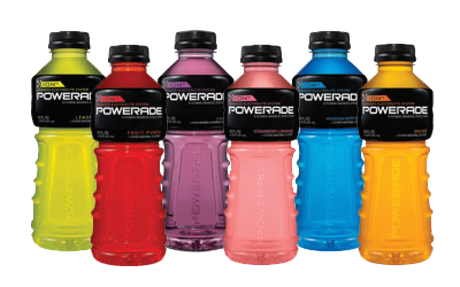
Powerade black colour traditional sleeves: a nightmare for Label presence Inspectors based on common photoscanners. We increased to 8 the amount of Photoscanners looking each one sleeve, discovering they were still not enough to assure the performances expected by Coca-Cola® and common sense. Still 2 % false rejects also with 8 rather than the original 4 Photoscanners
In a common general purpose digital output (on-off) Photoscanner, a nearly conic beam of infrared light is transmitted by a red or Infrared LED. Objects receiving this light diffuse it in all directions. A phototransistor existing in the front of the Photoscanner, receives a small portion of the diffused retro-reflected light. Its output signal enters an Operational Amplifier or a simple transistor acting as amplifier. Particular cares have to be devoted when applying this solution to the Label Presence Inspection. Our packagings are not flat surfaces and our labels or sleeves could be extremely dark, like the black Powerade® of this Case Study (image credit Datalogic, 2014)
Physics before
Before to endorse this “theory” we considered that all technological observed facts happen in the framework of the Physical Laws. They can be predicted, when due to known Laws. On the opposite, they are considered just Noise when are effect of Laws still not fully encased in ours standard models of the Nature of today. Knowing about the existence of this epistemological conundrum, first of all we searched for the Photoscanners' Data Sheet. The complete listing of all informations about that Detector, made public by its Vendor. Two of them, particularly relevant in the present Case Study, are:
- centre of the waveband of the Photoscanner light emission;
- detection diagrams, showing the response curve
Refer to the electromagnetic spectrum visible in the figure below. The “theory” precedently endorsed as that one showing good explanatory power for the observed facts, had been assuming that the electromagnetic energy at thermal frequencies (microwaves and infrared) irradiated by the Warmer Machine, be part of that range detected as a Signal by the Photoscanners. Thus superimposing the Warmer Machine radiation to the infrared retroreflected by correctly applied sleeves.
Contradiction in the temptative Root Cause
We felt a contradiction in this temptative Root Cause model. Thermal radiation of the Warmer Machine could have been really emulating non existing labels, creating the named False Negatives. Bottles without sleeve, falsely measured sleeved because of the abnormal inflow of thermal radiation, emulating a diffusing or reflecting sleeve correctly applied. But, to the amazed eyes of all of Us there, what was being falsely rejected were just the correctly sleeved bottles, say the False Positives. Exactly the opposite than the False Negatives. An evident contradiction in the temptative Root Cause model.
Focus on the Detector
We started to suspect that the Photodetector’s Margin was not enough. “Margin” is defined as the measurement of the amount of light from the light source detected by the receiver, expressed as a multiple of the minimum amount of light level required to switch the sensor output. Then, a margin of 2x is reached when the light level received is twice the minimum required to switch the output. All sensors should be operated at a margin greater than 2x. Detection of a low reflectivity target notoriously requires sensors with higher margin: higher Quality sensors.

The portion of the electromagnetic spectrum named Infrared (IR)
Refer yourself to the Data Sheet for the Photoscanner at right side (click-to-enlarge). Not the model of the Case Study, rather a more modern model whose performances are a bit superior.
Visibly:
- light emission is Infrared, centered at a wavelength of 880 nm (see figure below) as imagined by who thinked the Warmer Machine function being Root Cause of the malfunctions in the Inspector;
- detection diagram hints to another property (label colour and reflectivity). Showing, as an example, that a grey colour (flat) surface at 10 cm of distance provides the top of the detected signal. A distance which is doubled ito 20 cm if the surface is white colour, then more reflective;
- detection diagrams are always and only referred to a flat surface and not to a curved one, like a sleeve applied to a bottle. Implying that the amount of retro-reflected electromagnetic energy had surely to be lower than that, in our special beverage packaging inspection case. Lower than that meaning, as an example, that a grey coloured sleeve had to be optimally detected at a distance lower than 10 cm and a white sleeve, at a distance lower than 20 cm.
Focus on the packaging
We started to suspect that the true story be completely different than that originally imagined. One time removed the cardboard, discovered no marked effects of its absence: same unacceptable fakse rejects (~50 %). This excluded immediately the interferential scenario thinked by Third Parties. We ordered four additional Photo- scanners, identical to those originally present and set them like in the figure at right side. Why ?
Because our sleeves are:
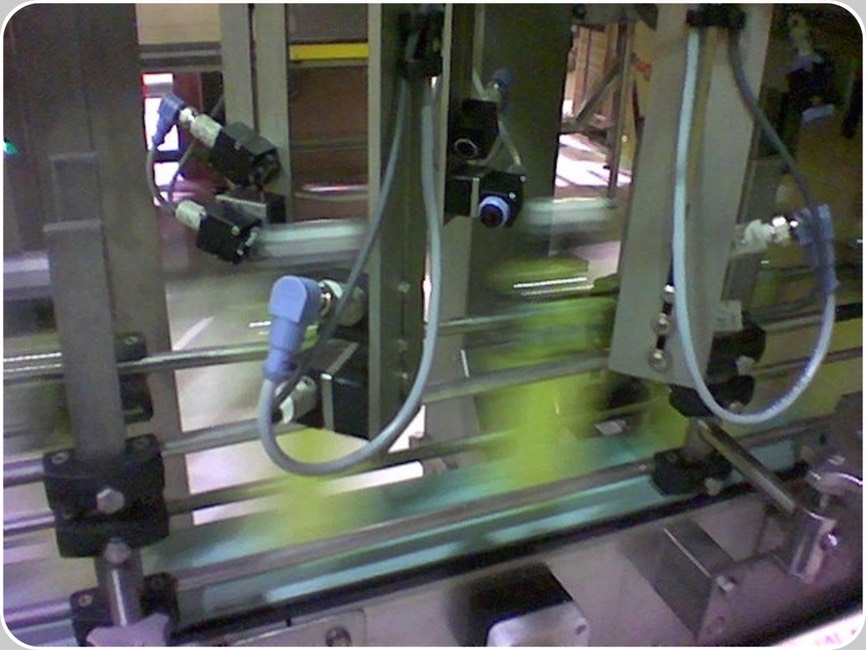
“All sensors should be operated at a margin greater than 2x (x, the minimum amount of light necessary to switch).
Detection of a low reflectivity target notoriously requires sensors with higher margin: higher Quality sensors”
- black and not grey colour, then less reflective;
- curved and not flat, then reducing the amount of electromagnetic energy retro-reflected into the phototransistor of the Photoscanner, the semiconductor device whose output signal is typically the input of an operational amplifier.
Powerade® sleeves are black and not grey colour, then less reflective. More, they are curved and not flat, then reducing the amount of electromagnetic energy retro-reflected into the phototransistor of the Photoscanner, the semiconductor device whose output signal is typically the input of an operational amplifier. Also 8 photoscanners resulted insufficient to commission the entire range of Powerade® products
And it get out that also 8 photoscanners resulted insufficient to commission the entire range of Powerade® products. If before the false rejects were ~50 %, now they were reduced to 2 %. A twenty-five times amelioration but, try to imagine an Aseptic PET Bottling Line not in one of those countries where it is possible to hire twenty people just to compensate the malfunction of one of the Machines. 2 % of 10000 bph are still ~100 bottles per hour and the reject accumulation table could not host so many containers without an Operator permanently there discharging it to prevent jams and Bottling Line stop. What else could we make to solve the problem ? Surely, installing 16, 24, or …100 Photoscanners should have solved the false rejects' problem. But, it’d also have created an opposite problem: overexposure. Rather than false rejects (False Positives) several unsleeved bottles erroneously considered sleeved (False Negatives), then a problem worse than the present of 2 % false rejects. Bottles without the sleeve going to the Market.
Root Cause: Project-related
The Root Cause of this unsolved problem, unsolved because it really remained there many years, is Project-related. Further investigations showed that the Project Management of the Vendor who sold the Electronic Inspector, never received samples of Powerade® sleeved bottles. Implying the negative effects were not caused by an error of the Electronic Inspector Vendor. The truth was that out of the USA Powerade® was a product so new that it was not possible for the OEM to let these samples be readied in time for the Vendor’s testing. Also, the Coca-Cola® franchisee who bought the entire Aseptic filling Line, on its side, then could not provide in useful time to the OEM samples to be forwarded to the Vendor. We were going to produce that special kind of beverage, there and then for the first time in that Country. It is a loophole along the Project sequence what created the unsolved problem. To fix it it’d have been necessary an investment. A different kind of electronic inspection system equipped with at least two cameras; as an example, a final inspection system, an equipment costing around four to five times that Label Presence Inspector.
Links to other Case Studies:

IntroductionIn the following, we’ll introduce the study of a pattern observed worldwide in the period 2005-2014 in the operative reality of around one-hundred Electronic Inspectors sold to be operated…

Case Study Sampling Table always jammedIntroductionTypical problems in a Food and Beverage Bottling Line derive by missing materials like motors, Frequency Converters, detectors, etc. In the following we’ll briefly study a Case where the “material” was much more than necessary. …
Case study 27% rejects stopping all days a Beverage Bottling Line The rejects' accumulation table of an Electronic Inspector in a Beverage Bottling Line, as it appeared to the eyes of the Operators and Management along 6 consecutive months after the day of the Line startup. …

Case study 1 Year of Production lost   In the following a case where the Machine blamed by the Bottler never functioned correctly since the first day. 18 months later, and after two different analysis made by elements acting in conditions of …

The “Device” Fusing, considered the Root Cause of whatever explosion, is just one superimposed component of an extremely longer sequence of conditions before and after, greater and smaller, than the Fuzing. …
IntroductionPowerade™ is a famous energy beverage, the first in a row of energy drinks with great success launched in the World, after 1988. Some years ago, The Coca-Cola Company™ updated the bottles of the standard Powerade to a new sport-grip bottle. …

Case study Cap presence control of sensitive beverages in 2001“X” is a great dairy filling and packaging plant. Here were installed, started and commissioned two standalone Full Bottle Inspectors in a new Aseptic Line for PET-bottled dairy products. …

Case study Cap Presence control of sensitive beverages in 2010Introduction “Y” is a great dairy filling and packaging plant. Here it has been installed a standalone Full Bottle Inspector in a new Aseptic filling Line for PET-bottled dairy products. …

Case study99.5% of the Non-Labelled Bottles sent to the MarketThe Technical Guarantees all Vendors provide to their Customers implies limits to their duties. What is into those limits is the area where, on the opposite, the Customer can exercises its rights. …

 IntroductionNo one of us has X-Ray's radiographic eyes. Because of this obvious reason, the cans’ content cannot be visually verified if, due to any reason, the Full Can Inspector is not active. …
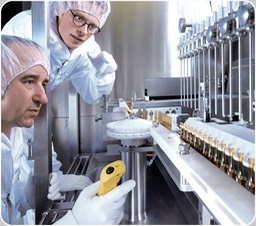
Case Study Electronic inspection of Pharmaceuticalsin-the-Machine-Cycle When speaking of guarantees of asepticity, Pharmaceutical Industry is since many decades what really retains the maximum know-how. …

IntroductionThe Pharmaceutical field is the origin of the technologies adopted today in the Aseptic filling, closing and inspection of beverages without any added preservatives. Are the Food and Beverage Packaging standards competing with the Pharma standards of, as an example 10 years ago ? …

Case HistoryGold-made electronic cardsImagine two huge cases arrived to your store today, filled with the spare parts you ordered and waited for 4-6 months. Electronic cards and other parts urgently needed to let your Machinery produce in Quality and Safety. …
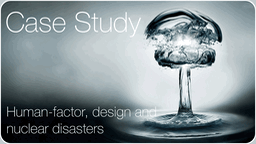
What Root Cause Analysis’ names human-factor plays a decisive role. A role made decisive as Root Cause of the majority (over 50 %) of all of the incidents registered in the productive processes. …
- Expensive in-the-Machine Electronic Inspectors reduced to cheap Standalone
- Sampling Table permanently jammed
- 27 % rejects stopping all days a Bottling Line
- 1 year of production lost
- SAFF-sequence Topology
- The Cardboard Label Inspector
- Cap presence control of sensitive beverages in 2001
- Cap presence control of sensitive beverages in 2010
- 99.5 % of the non-labelled bottles to the Market
- Canning Line's Layout relevance
- Pharma’s in-the-Machine-Cycle electronic inspection
- Leaking Pharmaceutical Containers
- Gold-made electronic cards
- Human-factor, industrial design and nuclear disasters
- A seismic Incident
- Filling Level Technical Guarantees
This website has no affiliation with, endorsement, sponsorship, or support of Heuft Systemtechnik GmbH, MingJia Packaging Inspection Tech Co., Pressco Technology Inc., miho Inspektionsysteme GmbH, Krones AG, KHS GmbH, Bbull Technology, Industrial Dynamics Co., FT System srl, Cognex Co., ICS Inex Inspection Systems, Mettler-Toledo Inc., Logics & Controls srl, Symplex Vision Systems GmbH, Teledyne Dalsa Inc., Microscan Systems Inc., Andor Technology plc, Newton Research Labs Inc., Basler AG, Datalogic SpA, Sidel AG, Matrox Electronics Systems Ltd.