Introduction
When discussing elsewhere the High Frequency fill level inspection, we also examined the complex mechanism of interaction between the High Frequency (HF) electromagnetic waves (3 - 30 MHz) and polar liquids like water. HF fill level inspection adopts a quite standard 21 MHz frequency. The same operative principle can be applied to the control of eventual residuals of water (plus, eventual traces of caustic soda) into bottles reaching the Empty Bottle Inspector by the Bottle Washer Machine. In this case, the frequency is lower, and typically ~4 MHz. The frequency-related phenomena observed after powering an High Frequency generator connected to an antenna in the air, whose fundamental is a continous wave (CW) at 4 MHz (subject examined in the fine-details here). In that section they have been analysed the effects measured by the probe of an oscilloscope emulating a receiving antenna. Described what is observed increasing the frequency from 500 Hz to 750 GHz. Yet for a frequency of only 250 kHz the macroscopic effects of the relation between a common RLC-serie resonant circuit (Resistor-Inductor-Capacitor) and its Environment, can be measured and registered. For all those accustomed to operate in the range of frequencies until 20 kHz: the World is completely different at 200 kHz. At 4 MHz all these relations results over ten times stricter. This is the main key of comprehension of the peculiarities and limits of the High Frequency Residual Liquid inspection. As an example, it allows to understand why:
The electromagnetic field intensified due to the peculiar solenoidal shape of conductor crossed by electrons, reveals itself by mean of the Iron filings oriented along the magnetic flux lines of force
- it should be possible to operate an EBI with a HF Residual Liquid inspection rejecting 2 ml of water with a detection ratio of 99.9 % and associated false rejection ratio < 0.01 %, ...incurring later in macroscopic false rejects, as huge as to stop completely the Filler Machine;
- when adjusting a HF Residual Liquid inspection to reject 8 ml of demineralised water with a detection ratio of 99.9 %, the associated false rejection ratio results always much higher than contractual < 0.01 %;
- HF residual Liquid inspection shows a rejection curve with an unexpected periodicity, after observing its entire serie of measurements registered along last twenty-four hours. This, front of bottles infeeding the Empty Bottle Inspector with the same identical amount of water in the base (i.e., 1 ml) along the same period.
Same issues we have presented elsewhere in these pages, comparing the different technologies for the Fill level inspection. Speaking of Fill Level inspection, it is really possible to eliminate all of the issues simply avoiding the poor-performant HF Fill Level inspection and adopting the X-rays' Fill Level inspection. But, in the presently discussed case of the HF Residual Liquid inspection, no alternative technology exists !
A permanent magnet evidentiating the spatial extension of a fixed magnetic field. The Iron filings oriented along the magnetic flux lines of force
Operation Principle
Bottles’ bottoms cross the space the electromagnetic waves irradiated by a Transmitter. Presence of water changes abruptly the intensity of the signal otherwise received. In the Receiver, the HF signal interferes with a second one whose frequency is ~470 kHz lower.
The resulting intermediate frequency signal is then transferred to the processing electronics and there digitized. Later, digitized values are compared to limit values, allowing to reject values out of the admitted range. Presence of caustic soda, a residual by Washer Machines process, also in small traces < 1 %, strongly enhance the resulting signal and then the probability to detect the defective bottle. The presence of caustic soda, a residual by Washer Machines process, also if limited to small traces with density < 1 %, enhances the resulting signal and then the probability to detect a defective bottle.
The Bottle Washers Machines assure a near-sterilisation of the glass returnable bottles (GRBs) by mean of a serie of baths where caustic soda density reaches ~ 3.8 %. In the figure, the caustic soda tanks part of the Clean-In-Place (CIP) of SABMiller Plc Brewery, Nigeria ( Tom Parker/OneRedEye)
In the red circle evidenced one of the two modules of a High Frequency Residual Liquid inspection with the bottles passing thru them, moving left to right. A module is a RF TX at 4 MHz, the other a RF RX for the same frequency, followed by a RF generator set at ~3.5 MHz. The net result is to move only relatively low frequencies along the connection cables, avoiding losses and interferences
Advantages
- 2 mm of water over the top of the convexity of bottles’ base bottoms, are commonly detected > 99.9 %;
- false rejects < 0.01 %;
- easy of use.
Molecular arrangement of the crystal form of the Sodium hydroxide (NaOH) also named caustic soda, or lye (
Qubik, reproduced under CC 3.0)
Disadvantages
The main issue associated to all these systems is the dependance of their response by the ambient humidity and pressure. On practice, the same issue affecting all High Frequency fill level inspections. With the big difference that at least all Full Bottle Inspectors may be equipped with the optional Thermal Compensation module. What cannot surely be made in the Empty Bottle Inspectors.
In the meantime, as a matter of fact, to the date no one Vendor of Electronic Inspectors realized the opportunity to linearise the high frequency circuit response with respect to the ambient conditions:
- relative humidity;
- temperature.
And the result is that the digits expressing the performances declared by all Vendors (2 mm of water over the top of the convexity of bottles’ base bottoms, are typically detected > 99.9 % with false rejects < 0.01 %) are grossly exaggerated when compared with the 24 hours natural cycle. At 5 AM the humidity could start to condensate over parts, reducing their impedance. At 2 PM, on the opposite, we’ll have maximum temperature and its effect over humidity. On practice, a different value for the impedance of the same identical glass bottle, filled with the same identical amount of distilled water. The net result of all this is that also in the HF Residual Liquid control, exactly like in the HF Fill Level Inspection, a single sensitivity adjustment cannot cope with the continous changes of the impedance of the resonant circuit. Setting a sensitivity coherent with the rejection of:
- 2 mm of water over the top of the convexity of bottles’ base bottoms > 99.9 %;
in the following days we’d be the unhappy Spectators of:
- false rejects >> 0.01 %,
typically ~0.2 %. And it is because of this reason, that also in the Empty Bottle Inspector visible in the figure above there are two separate and independent HF Residual Liquid Controls, rather than the one visible in the red circle. The second lying out of the final inspection system, immediately before the Rejector deviating defective bottles to the Bottle Washer machine. This way, adjusting two systems at a moderate sensitivity, it results possible to keep the performances aligned over the Contractual:
2 mm (millimetres, not milliliters) of water over the top of the convexity of bottles’ base bottoms, detected > 99.9 % with false rejects < 0.01 %.
And If We’d Use 3 Modules?
Considering the relevance of this inspection, due to the presence of a Machine (the Bottle Washer) continously introducing water and caustic soda into bottles, we’d be tempted to extend the precedent line of reasoning. Then, Readers could start to ask themselves about the possibility to add a third HF Residual Liquid Control to their EBIs. The reality is that the solution of the problems deriving by the use of High Frequency electromagnetic waves like measurement instrument, lies only in the linearisation of the circuit function with respect to environmental conditions. As a matter of fact, when compared to the entire electromagnetic spectrum (see figure below) what we name “High Frequencies” are relative “low frequencies”. Following Planck’s Law, so low energetic to be unavoidably related to the environmental conditions.
A benchmark of four different fill level technologies. γ-rays, X-rays, Infrared (IR) and High Frequency (HF) in the electromagnetic spectrum, based on the energies involved by mean of the E = h v fundamental formula (where v = c / λ, c speed of propagation of em waves in the vacuum, λ wave length, v frequency, h Planck's constant, E energy of the photon). In the case of the Bottling Controls the energy of a single γ-ray photon results ~ 100 000 000 000 times greater than that associated to an High Frequency (HF) at 21 MHz. This, in turn, explains why all High Frequency controls are so exposed to ambient conditions and false rejects ( CC 3.0)
Recommendations
- Always order the new Empty Bottle Inspectors configured and equipped with two HF Residual Liquid inspections;
- always upgrade the existing Empty Bottle Inspectors so to become equipped with two HF Residual Liquid inspections;
- always keep in your store the couple of parts particularly exposed to damage, the Receiver and the Transmitter, installed a few millimeters only far from the bottles’ passage. The Vendor-declared MTBF (Medium-Time-Between-Failures) refers to parts fault not because of external causes. One time installed in a running EBI, the risk these parts are damaged by water sprayed by an Operator, or because a connector or cable are damaged by broken cutting glass bottle splinters, is very high. If you have your Bottling Line reduced without a single operative control for water + caustic soda, that is not the right time to handle discussions about parts’ guarantee, spare parts’ purchasing and arrival of a spare part. That is simply too late.
Links to other pages:

What Container Empty Bottle Inspectors (EBIs) and the related measurements whose goal is a binary classification (collectively named inspections), are a category making a particularly sensitive activity: to protect final consumers' health, assuring beverages' safety in the Food and Beverage Packaging Lines. …
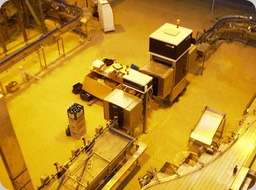
Rotary-Linear EBI ComparisonRotary EBIThe Empty Bottle Inspectors of the past were always and only Rotary Machines. The industries which first started to design and produce them and those which adopted them, were all US-based and specialized in the production of glass bottles. …
Introduction When discussing elsewhere the High Frequency fill level inspection, we also examined the complex mechanism of interaction between the High Frequency (HF) electromagnetic waves (3 - 30 MHz) and polar liquids like water. …
Introduction It is a fact: when bottles are urgently needed, also glass returnable bottles born to host beer or mineral water, can fulfill their basic purpose of container for liquids of completely different nature. …
Introduction Base inspection is the most important at all and also the first historically created for EBIs. In the start, it was applied to small inspectors used by glass bottles Producers. It is always present in the Empty Bottle Inspectors, as a minimum standard, jointly with a few others like the High Frequency Residual Liquid control and the Finish inspection.

A common PET bottle as visible with (right side) and without (left side) polarising filtering. At right side, cellophane in the stripes around the bottle rotates the light polarization vector (  …
Introduction The term “finish” originates with the mouth-blown bottle production process where the last step in completing a finished bottle was to finish its lip. Today, the lip or finish is the first forming step in the bottle making process. …

Operative PrincipleThe operative principle of the Finish inspection is applied, in a similar way, to the more complex case of check of the status of the glass threads. In this case, light is generated by an illuminator on top of the finish. …
In the Linear Glass Returnable Empty Bottle Inspectors, External Sidewall Inspection may be performed adopting one or two CCD-cameras. We’ll treat in the following the application with two CCD-cameras: single-camera applications are not satisfactory, covering only < 80 % of the external surface of the bottles.
Why Inner Sidewall InspectionThe inner surface of the bottle may host larvae, insects and other low-contrast foreign objects whose detection, as seen by the External Sidewall is nearly impossible. …
IntroductionThey exist defects no Bottle Washer shall never remove, whatever the duration of its cycles, the amount of caustic soda or temperature of the water. Between these:Paint, internal or external;…

IntroductionScuffing is a memory of the many passages of the returnable bottle thru the Bottling Line, mainly of the wearing of its external sidewalls after friction with other adiacent bottles. …
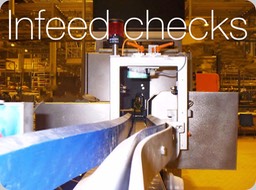
Infeed ChecksEmpty Bottle Inspectors always need to be protected by prior controls and rejector, to prevent damages implicit in their operation. Damages originated by: fallen bottles, inclined bottles, …
IntroductionTo perceive the rationale for the inspection of the bottles’ colour, we recommended to take a look at the figure on right side. That is what a Customer considered “a bottle format”. …
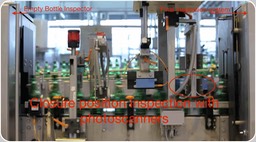
Closure inspection by digital Photoscanners(to be continued)Links to other pages:  This website has no affiliation with, endorsement, sponsorship, or support of Heuft Systemtechnik GmbH, MingJia Packaging Inspection Tech Co., Pressco Technology Inc., miho Inspektionsysteme GmbH, Krones AG, KHS GmbH, Bbull Technology, Industrial Dynamics Co., FT System srl, Cognex Co., ICS Inex Inspection Systems, Mettler-Toledo Inc., Logics & Controls srl, Symplex Vision Systems GmbH, Teledyne Dalsa Inc., Microscan Systems Inc., Andor Technology plc, Newton Research Labs Inc., Basler AG, Datalogic SpA, Sidel AG, Matrox Electronics Systems Ltd.
- EBI Classification
- Linear and Rotary EBIs
- High Frequency residual Liquid control
- IR Residual liquid control
- Base inspection, opaque defects
- Base inspection, transparent defects
- Finish inspection, crown cork
- Finish inspection, broken Thread
- External sidewall inspection, for opaque defects
- Inner sidewall inspection for opaque defects
- Mineral ring inspection
- Scuffing inspection
- Infeed checks
- Colour inspection
- Closure inspection with digital photoscanners
This website has no affiliation with, endorsement, sponsorship, or support of Heuft Systemtechnik GmbH, MingJia Packaging Inspection Tech Co., Pressco Technology Inc., miho Inspektionsysteme GmbH, Krones AG, KHS GmbH, Bbull Technology, Industrial Dynamics Co., FT System srl, Cognex Co., ICS Inex Inspection Systems, Mettler-Toledo Inc., Logics & Controls srl, Symplex Vision Systems GmbH, Teledyne Dalsa Inc., Microscan Systems Inc., Andor Technology plc, Newton Research Labs Inc., Basler AG, Datalogic SpA, Sidel AG, Matrox Electronics Systems Ltd.